Farine fossili per la filtrazione nella produzione vinicola
Trentino wine from Cantine Mezzacorona
Literally, the roots of Cantine Mezzacorona have been firmly rooted in the terraces and plains of Trentino Alto Adige for over a hundred years. Since 1904 generations of local families decided to combine their vineyards to enhance the value of their grapes, resulting in increasingly natural and healthy wines that respect the environment. Today, 2800 hectares are cultivated by more than 1600 members, with a turnover of more than one hundred million euros. Nevertheless, the basis is still the manual processing of the grape fields, combined with innovative and sustainable production techniques. Cantine Mezzacorona holds the leadership in bottling Pinot Grigio, Chardonnay and Gewürztraminer among the white grapes and Teroldego, Rotaliano and Lagrein for the red ones. Cantine Mezzacorona has entrusted our company with a modern pneumatic transport system that allows the handling of kieselguhr in its cellars.
What is kieselguhr
Kieselguhr has several names because, as well as in enology, it is also used in many fields such as agriculture, pharmacy and even as an insecticide. It is also called diatomaceous earth, diatomaceous sand or diatomite. It is essentially an organic sedimentary siliceous rock, created as the fossilised residue of single-celled marine algae of the diatom family, which appeared on Earth around 145 million years ago. Over the ages, these algae have formed immense deposits of microscopic siliceous shells in lake environments, with diameters of a few microns. Kieselguhr is the most commonly used filtration aid, both because of its grain size, which is smaller than sand, and because it is very porous. It is in fact used together with standard filters to increase their filtering efficiency.
Filtering in wine-making
In wine cellars, wine filtering is a common practice and is carried out at various times during production, mainly in the early stages to eliminate residues from the processing of the must before fermentation, but it is also useful after refrigeration, during pasteurisation and before bottling. Depending on the purpose of the process, the techniques and filters vary: there are continuous flood filters or plate filters or even membrane filters, made of cloth, cardboard or other materials.
In our case, the pneumatic conveying system we created is designed to feed a filter press, an industrial machine that separates the liquid from the solid. The filter press has inside a series of perforated stainless steel plates and frames that alternate, also interspersed with filtering layers. The four corners of each plate and frame are perforated so that, when the machine is compressed, the wine to be filtered can flow through them and the filtered liquid can then drain off. The wine is filtered thanks to the pressure difference between two adjacent areas of each filtering layer and is conveyed from the draining surface of the plate to the outlet pipe.
Pneumatic conveying plant for kieselguhr
The pneumatic transport plant is fed by a big bag emptying system, also supplied by our company. This is a system that allows the use of huge bags of kieselguhr, weighing up to 2000 kg. By being able to process such large sacks, the winery will also save on the purchase of kieselguhr, and the pneumatic system feeding the filter press can run for a long time without having to think about recharging. The big bag emptying system consists of a steel frame with a fastening system at the top. This is where the big bags are secured in order to keep them taut. In the lower part the big bag rests on a stainless steel cone with a door for manual opening of the bag. Underneath this cone is the valve unit that regulates the flow of kieselguhr into the pneumatic conveying system.
The loading hopper is made in AISI 304 stainless steel, internally and externally satin-finished, equipped with a curved fitting for connection to the suction unit by means of piping in non-toxic and antistatic material. Internally it is equipped with a polyester bag filter class M+L which is cleaned by means of a pneumatic filter shaker. Exhaust system by means of a butterfly valve with AISI 304 stainless steel lens and aluminium body, complete with double-acting pneumatic actuator.
With this pneumatic conveying system it is possible to feed the filter presses in a continuous and controlled manner, automatically supplying them with kieselguhr whenever the kieselguhr has exhausted its filtering power and needs to be replaced. The main features of the plant are
- kieselguhr capacity up to 1400 kg/hour
- Transport length 4 m vertically and 15 m horizontally
- 5.5 kW electrical power
- filter surface area 0.9 m2
- air flow rate 550 m3/h
- depression 210 mbar
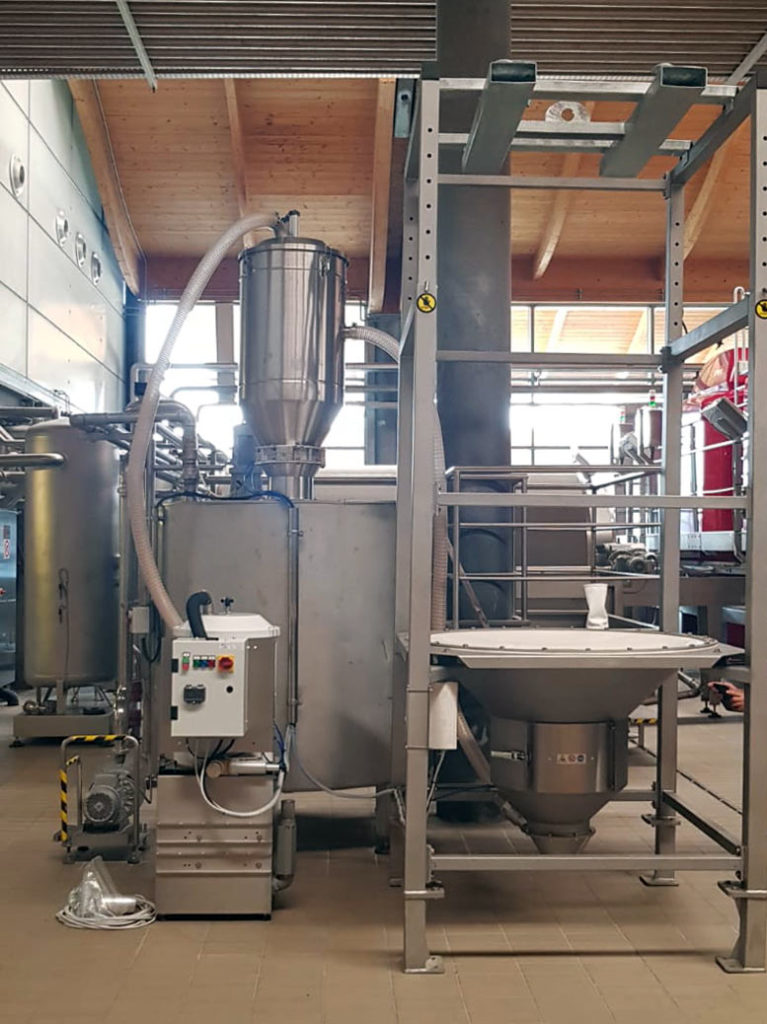
Pneumatic conveying system for fossil flours installed in a cellar, consisting of a big bag emptying system, loading hopper and suction unit.
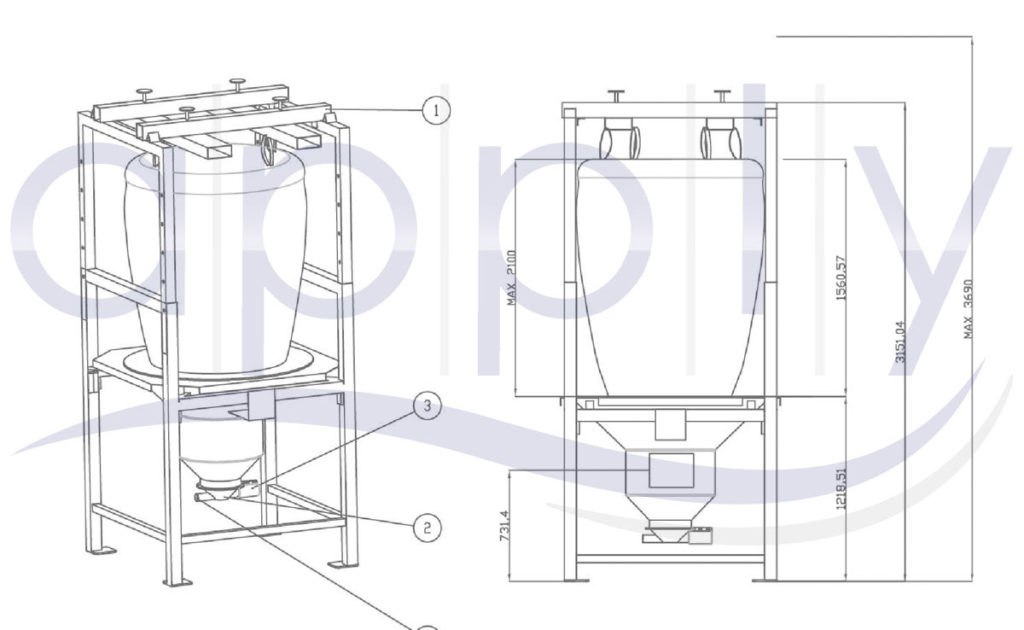
Technical drawings of a big bag emptying system feeding a pneumatic conveying system for kieselguhr.